Year of implementation: 2024

LINAPLAST
Industry: Plastics processing, tool production and automatization
Country: Czech republic
Customer´s website: linaplast.cz
Key benefits:
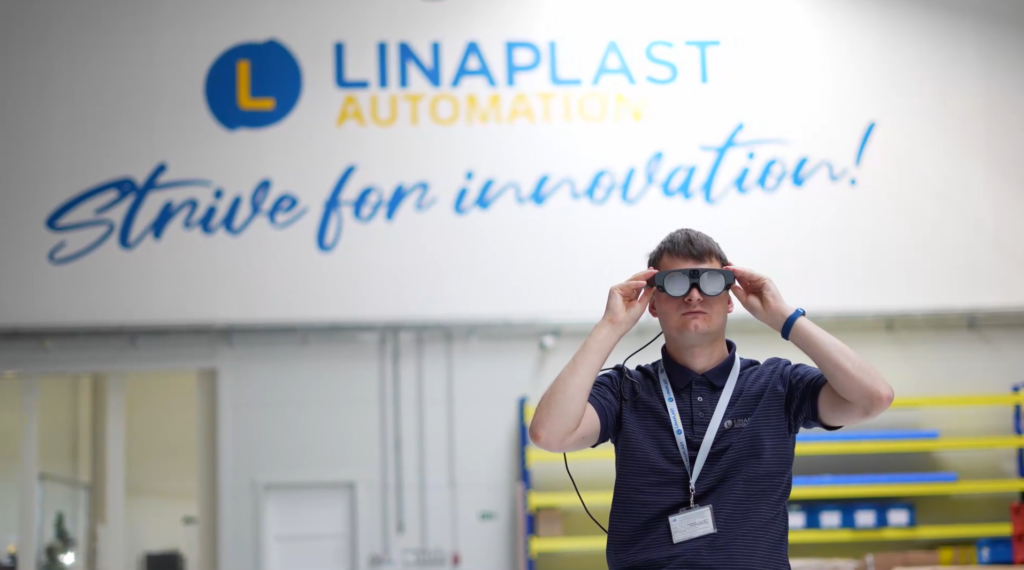
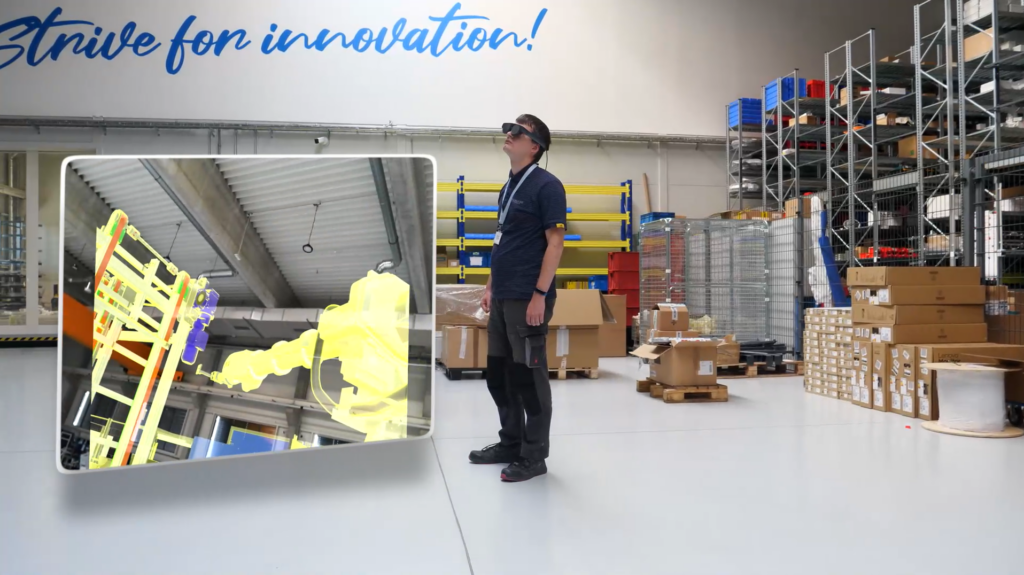
LINAPLAST at the cutting edge of innovation: Using XR technology for advanced 3D visualisation
For LINAPLAST, a turnkey plastics processing, tooling and automation company, we designed a comprehensive XR solution for detailed 3D visualization of large and complex machines without time-consuming preparation or data conversion. The resulting solution includes the implementation of Magic Leap 2 smart glasses, Space software and our professional services and support.
Choosing smart glasses as a strategic decision
LINAPLAST was looking for a technological solution that would enable a significant innovative advance in several areas. To get the right AR application for their needs, the company partnered with us as an XR expert.
We provided the company with support in selecting individual applications and presented in detail the various models of smart glasses, from which they then selected and tested the most suitable ones for use in their work processes. LINAPLAST needed a convenient and easy-to-use solution for displaying 3D data in CAD, without time-consuming model preparation. After deciding on the right solution, the actual delivery was quick with simple training.
Processes before implementation
Before the implementation of smart glasses, they used classical CAD software on the computer, where they could construct and visualize 3D models. However, this method did not allow for real space and size representation of the models. Assessing scale, accessibility and maintenance from a 3D model displayed on a 2D screen is complex and can lead to a lack of understanding of the product in tangible terms. This shortcoming makes it difficult to provide the specific feedback that engineers need to better tailor the product to customer needs.
Benefits of the new solution
The implementation of augmented reality (AR) for visualizing 3D models in real space significantly:
- streamlined development activities on concepts and design of production lines and equipment,
- reduced the cost of physical models and repairs,
- helped to show models of lines and equipment in real environments where they will later actually stand and be produced – showed the difficulties associated at the sites of later operation,
- increased the quality and accuracy of designs, through detailed visualisation and early identification of errors,
- enabled an interactive course of action (presentation and sales support) that increases customer interest and satisfaction.
Overall, AR has moved the company to the cutting edge of technological innovation and provided a competitive advantage through greater flexibility and speed in adapting designs to customers. Above all, ease of use is key for LINAPLAST, enabling employees to use the technology effectively. They can view the 3D model in full quality on their smart glasses in minutes, with no scene preparation or model optimization required. This is made possible by the unique Hololight Space software, which allows models to be displayed at their true size and with the same level of detail as a CAD file. Users perceive the simple manipulation of the 3D model, the interaction and wide range of views, the X-ray mode, measurements, the ability to extract individual components from the model and the placement of the 3D model on the base structure as the most important functionalities.
Ing. Karel Novotný, LINAPLAST’s Technical Director, confirms, “Visualizing our designs in AR and real-world settings helps us get valuable feedback from various stakeholders on what might need to be modified to better meet customer needs.”
The solution delivered has found applications in the following areas:
- Prototyping – accelerating development
- Design review – conducting internal design reviews in the team and with customers
- Factory layout planning – precise placement of the machine in the customer’s real space, thus verifying possible clashes with other objects and optimizing the layout of the work area
- Workplace ergonomics testing – gathering feedback from operators, technicians and maintenance
- Marketing and sales – interactive presentations and meetings
Vision and plans
LINAPLAST understands that immersive technologies are already standard in many industries and it is essential to use them to achieve maximum benefits.
We have now implemented two XR solutions together with LINAPLAST. The first involves augmented reality for visualizing 3D models in real space and the second provides remote support for their service team using assisted reality and RealWear glasses. LINAPLAST plans to continue to expand the use of these technologies into other areas of their service.
„Visualizing our designs in AR and real-world settings helps us get valuable feedback from various stakeholders on what might need to be modified to better meet customer needs.“
Ing. Karel Novotný
Technical Director
LINAPLAST