Year of implementation: 2023
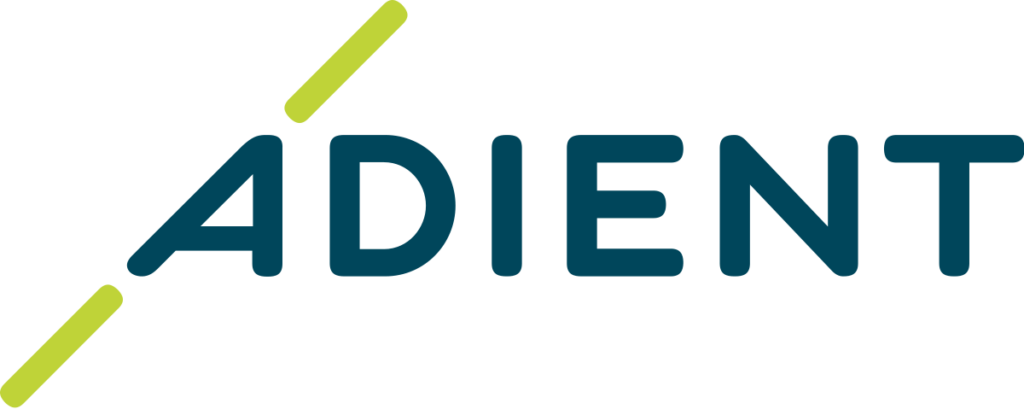
Adient
Industry: Automotive
Country: Czech Repuclic
Key benefits:
Effective operator training and process accuracy with smart glasses
Adient takes an active approach to new opportunities and is constantly looking for ways to improve workflows. The implementation of RealWear Navigator smart glasses into the employee training process and ensuring proper machine maintenance procedures was an innovative step towards digital transformation and efficiency.
As a global leader in automotive seating, Adient supports major automotive manufacturers to differentiate their vehicles with superior quality, technology and performance. The company’s Roudnice plant specialises in the production of car seats and is the spare parts centre for the whole of Europe. The implementation of smart glasses took approximately 6 months from the initial idea of acquiring the new technology. In a relatively short period of time, it has delivered several key benefits and savings.
Analysis and solution suggestion
Before implementing smart glasses, the company followed standard training processes that included watching videos and complex excel spreadsheets and lists. These procedures did not ensure that routine activities, such as independent maintenance of sewing machines, were performed consistently and correctly. All led to a reduction in performance and an increase in machine repairs.
The first step was to carefully analyse the process. Following this process, we tested various technological elements, including hardware and software, to guarantee optimum functionality and efficiency. After thorough testing, we made a final selection of the solution that best suited their long-term needs.
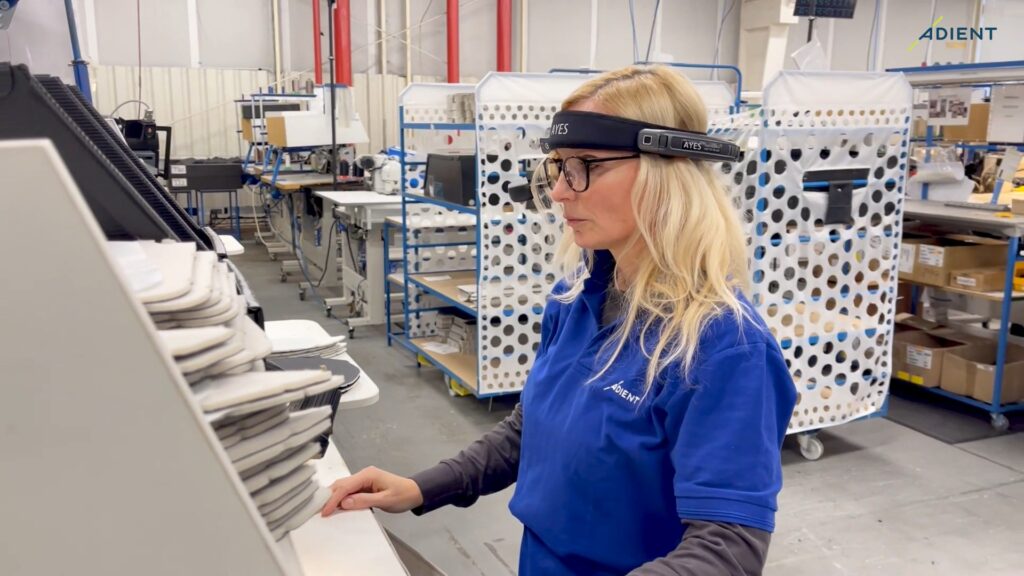
Why smart glasses?
The results show an increase in the efficiency of the training and maintenance process. Workers can see the digital workflows right in front of their eyes and are confident that they are performing all steps correctly. In addition, the technology has interactive voice control and digital storage capabilities, which was considered as a key to ensure ongoing records of each step.
The RealWear Navigator smart glasses were the most suitable solution due to their unique features such as already mentioned voice control, the integrated camera for recording and above all, the wide range of uses in various work positions. The easy fit on the head and the unrestricted field of view were important factors in choosing this technology.
12 points of self-maintenance: the TPM
The first project chosen for implementation was TPM, as it affects almost every employee in the organization.
The display of the glasses shows the different workflows and leads workers step by step to perform them correctly. The device is controlled by voice commands such as “continue”, “take picture”, “yes” and others. In addition, the operator has both hands free to work and is not limited in any aspect of the work. Thanks to smart technology, we have reduced process errors, streamlined the work and made it possible to carry out individual training in case of any uncertainties with digital recording.
It is important to point out that the control is really very intuitive. Thanks to the introduction training by AYES experts, the customer can easily create new training or maintenance procedures completely on their own. There are situations where the smart glasses completely replace or supplement the existing instruction videos and excel spreadsheets.
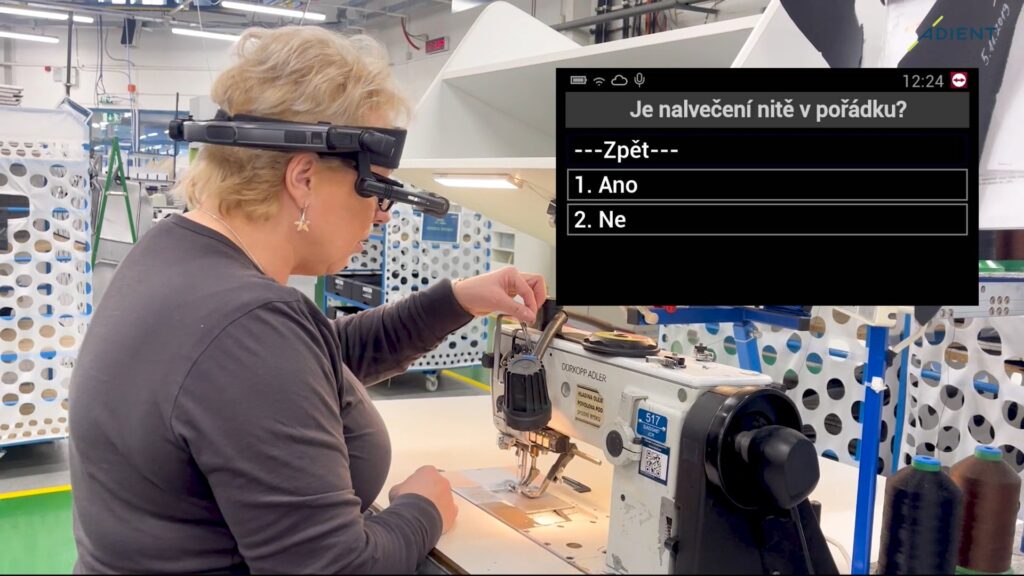
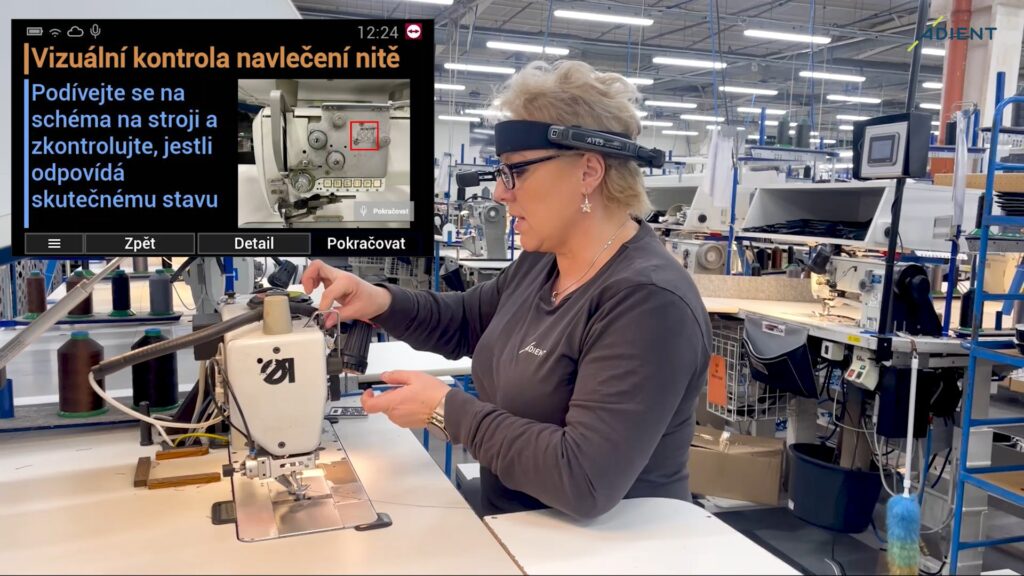
Benefits, plans and development
The smart glasses are comfortable, easy to fit and offer a wide range of uses across all job positions, including operators, mechanics, final inspection and warehouse workers. The company plans to expand the use of smart glasses to additional positions and projects.
Zdenek Reimann, Process Engineer adds: “AYES provided the smart glasses technology that reached Adient’s needs. Expertise and the ability to respond quickly to the company’s specific requirements were decisive in selecting a partner for this innovative project.”
The final evaluation of the entire project will take place in the coming months according to plant standards. Time savings, quality improvements and a reduction in unauthorized equipment repairs, reduced mechanic downtime, machine shutdowns and minimized downtime are expected.
“AYES provided the smart glasses technology that reached Adient’s needs. Expertise and the ability to respond quickly to the company’s specific requirements were decisive in selecting a partner for this innovative project.”
Zdeněk Reimann
Process Engineer
Adient