Year of implementation: 2023
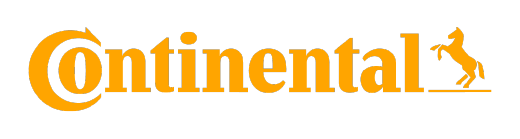
Continental Automotive Czech Republic
Industry: Automotive
Country: Czech republic
Customer´s website: continental.com
Key benefits:
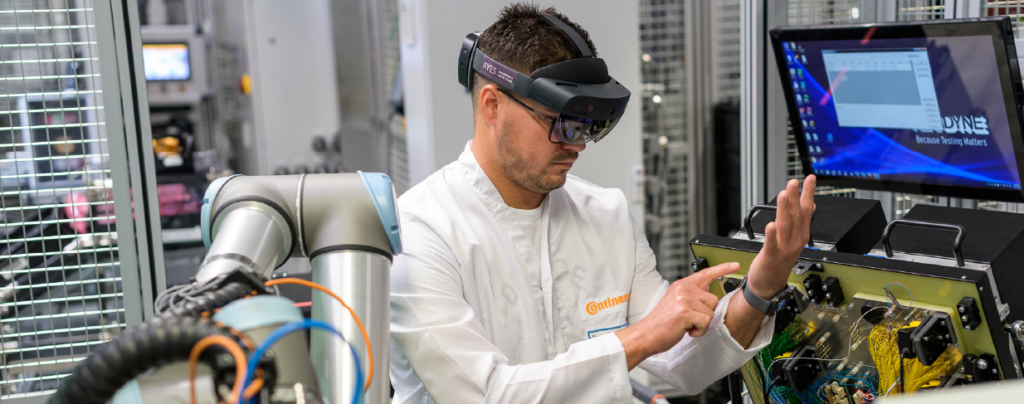
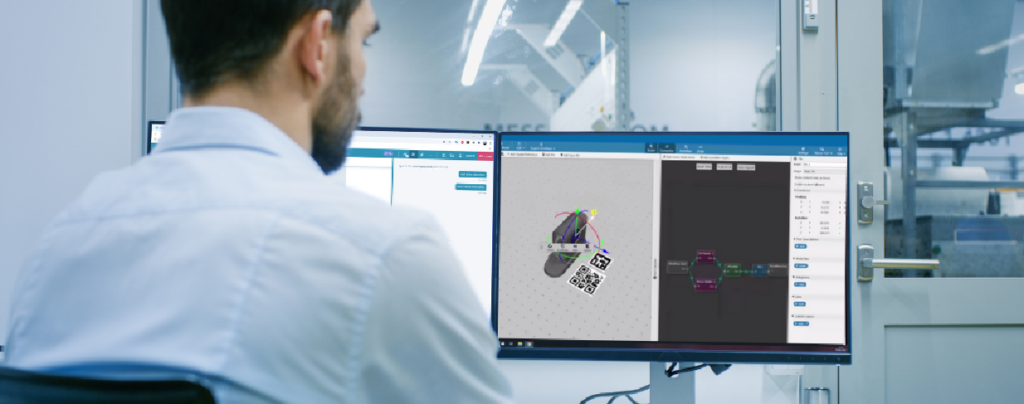
A modern approach to the training of operator on the production line using Microsoft HoloLens 2 smart glasses
AYES designed a customized, comprehensive solution for Continental Automotive Czech Republic to digitize workfows using Microsoft HoloLens 2 smart glasses and TeamViewer Frontline Spatial software. These are now helping to train operators on the new production line as part of a pilot project.
Continental Automotive Czech Republic is part of a German concern that manufactures rubber products and advanced technologies for the automotive industry. At its production facility in Brandýs nad Labem, the company produces large-format displays, car stereos, multimedia systems, air condition panels, eCall systems and fuel system control units. Nowadays, the Brandýs plant is globally the largest Continental electronics plant. Its customers include global automotive companies such as BMW, VW, PSA, Daimler, Renault, Fiat, Toyota and many others.
At the same time, the Brandýs nad Labem plant is a pioneer in the field of digitization, automation and robotization of production throughout the Continental AG Group. A dedicated Smart Automation team is systematically working on the digitization and automation of production lines and looking for ways to save operating costs. They also make use of modern technologies to do their work, including smart glasses for working in augmented reality.
AYES and Continental have been partners for augmented reality since 2019, when they began testing the first possibilities of using smart glasses in the production plant. This resulted in the successful implementation of RealWear smart glasses for remote support of maintenance staff with colleagues from engineering, and subsequently the use of the same technology for auditing the production lines remotely (Remote gemba).
Intelligent and tailor-made solution
However, for creation of digital workflows that help operators working at two sites of the new production line, Continental was looking for a different solution. One that would not only display text and images, but also more advanced animations and work with 3D models of the real components to be assembled by the operator. The solution tested for the pilot ended up being a combination of Microsoft HoloLens 2 smart glasses and TeamViewer Frontline Spatial software.
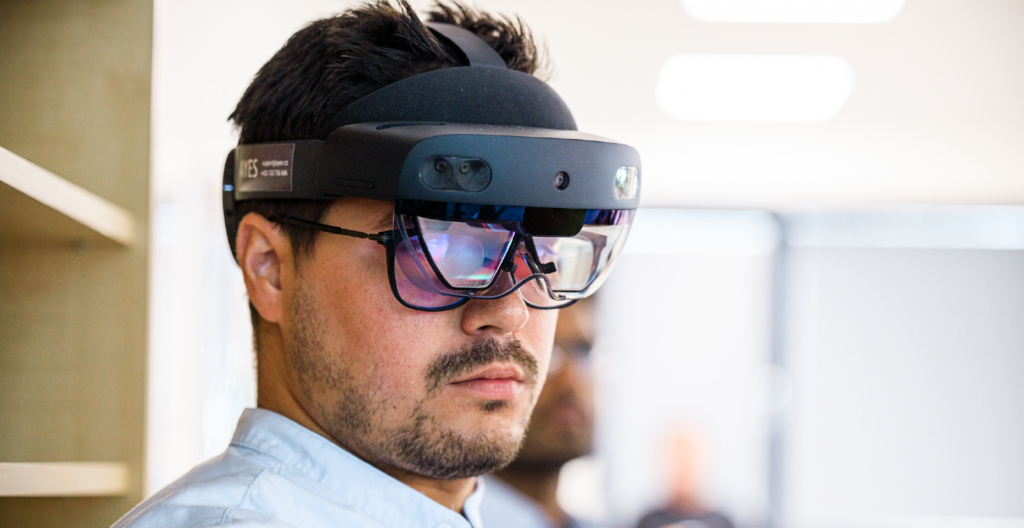
Microsoft HoloLens 2 alows you to wear your own dioptric glasses at the same time when using .
“We were quite clear in terms of hardware since the beginning. Microsoft HoloLens 2 is probably the most comfortable and technically best equipped device for work in mixed reality in industrial production at the moment. The battery lasts over two hours of continuous work, the glasses are lightweight and what is very important, you can wear your own dioptric glasses at the same time when using them. In addition, they can be shared between multiple users as they have automatic eye calibration. However, with the software, we weren’t sure which solution would be the best for us. We tested several options, but when AYES recommended TeamViewer Frontline Spatial for the pilot, we knew we had to deploy it,” explains Petr Bařina, Smart Automation Teamleader at Continental.
Intuitive – efficient – top class
TeamViewer Frontline Spatial adds 3D augmented reality capabilities to the Frontline platform. It is a very simple tool that has an attractive environment and its clear instructions and navigation make working in it intuitive and efficient. Therefore, after a short initial training, anyone can create high-quality 3D workflows without the need for advanced programming knowledge, and the preparation of digital workflows can be entrusted to less experienced staff, freeing up capacity for dedicated engineering teams
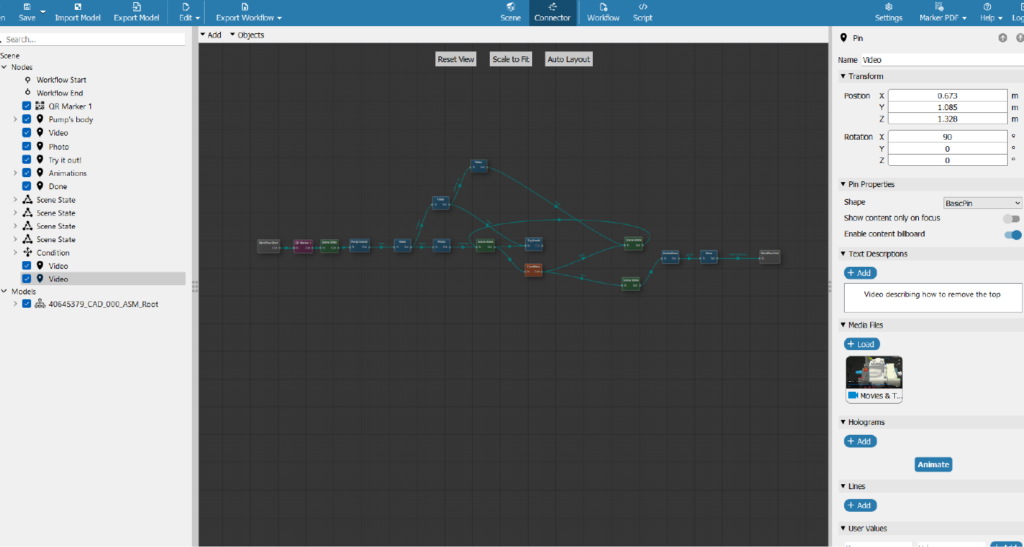
The preparation of the digital workflows is very intuitive and efficient..
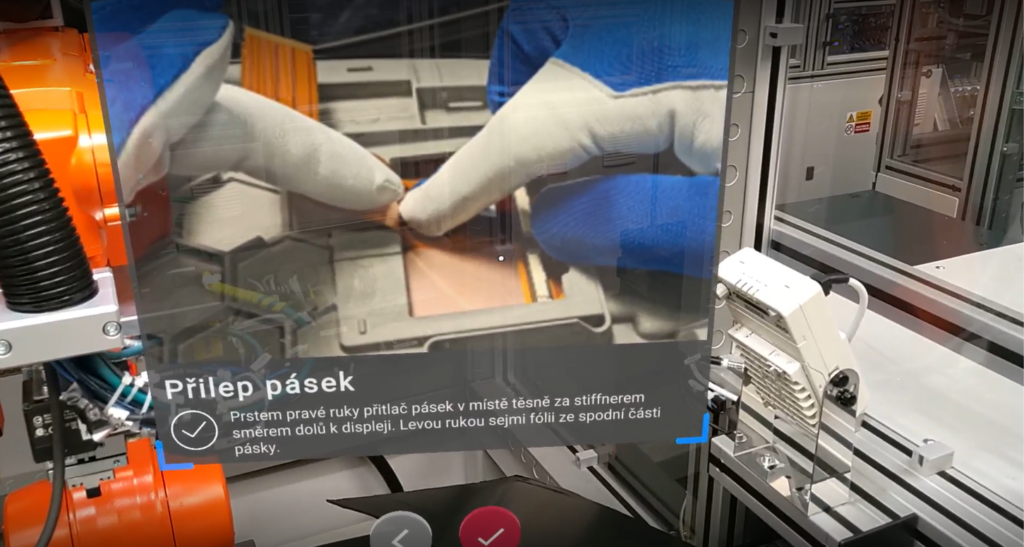
TeamViewer Frontline Spatial allows you to work with 3D models and create animations.
The software is fast and clear. Its indisputable advantage is that it allows different scenarios and schematics to be prepared, stored and subsequently used in one folder for one production line. Thus, one sub-folder can be, for example, a digital workflow, another can be a 3D preventive maintenance manual and a third can be a demonstration of the most common errors with instructions on how to solve them or prevent them.
One hundred percent customer support during preparation and ROI calculation
Before Continental decided on this solution, a thorough initial analysis had to be carried out in cooperation with AYES. Tomáš Vravko, Sales Director at AYES, adds: “A thorough initial analysis of the customer’s needs, including ROI calculations, is essential for the later success of the entire project and for the right selection of the technology. It´s not enough to simply purchase whatever hardware and software available on the market, if we really want both employees and the company benefit from it.. The needs vary greatly from business to business. At AYES, we are aware of this, and that´s why we always strive to provide our customers with solutions that are as tailored to their needs as possible.”
Just two days after the initial meeting, we already presented the solution to Continental, showing all the features and benefits, including a specific tutorial demonstration. At the same time, we prepared detailed training for dedicated employees so they would be able to prepare all on their own as soon as possible. “The speed of the preparation of the trial and the willingness on the side of AYES played a significant role in the selection of the supplier. At the same time, they assisted us in preparing the entire business case and helped us define all the areas where we could save money by purchasing smart glasses,” adds Petr Bařina.
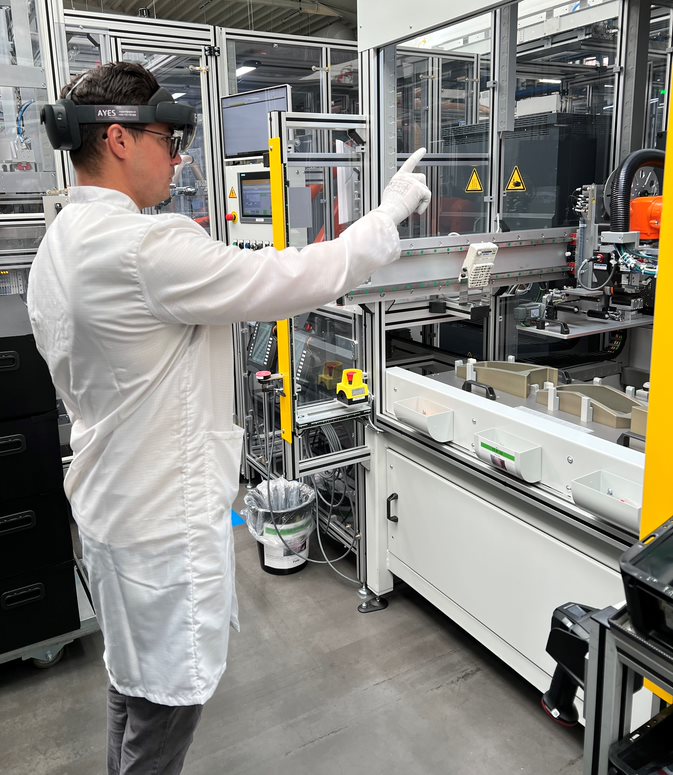
Verification and testing of the chosen concept is crutial for successful digitization of the production.
Visions and plans
Continental’s new production line is currently being finalised before going live, as are the digital workflows for operators. Proof-of-concept (POC) testing will take place until the end of 2023. During this period, the customer will verify the functionality of the solution and evaluate feedback from direct users. These findings will then be used and taken into account when deciding on the permanent deployment of the process. If the POC is successful, Continental has big plans for smart glasses.
The intention is not only to extend the technology with the assistance of the AYES team to other production lines within the Brandýs nad Labem plant, but also to standardise the solution across the Group and extend it to other production sites around the world. At the same time, they are already thinking about using it in other departments of the Brandýs plant. For example, the plan is to deploy Microsoft HoloLens 2 smart glasses in the maintenance team to train new team members so they can work independently on the routine tasks quicker. The 3D instructions will show them the sequence of individual tasks that need to be performed, and at the same time it will be possible to display selected parts of the machine in augmented reality, the most common errors on this part and their solutions to correct them.
„We were quite clear in terms of hardware since the beginning. However, with the software, we weren’t sure which solution would be the best for us. We tested several options, but when AYES recommended TeamViewer Frontline Spatial for the pilot, we knew we had to deploy it.“
Petr Bařina
Smart Automation Teamleader
Continental
„The speed of the preparation of the trial and the willingness on the side of AYES played a significant role in the selection of the supplier. At the same time, they assisted us in preparing the entire business case and helped us define all the areas where we could save money by purchasing smart glasses.”
Petr Bařina
Smart Automation Teamleader
Continental